Oil pipelines play a crucial role in the transportation of petroleum products from the extraction sites or refineries to various distribution centers. These pipelines span vast distances and are subjected to extreme conditions and environmental challenges. To ensure efficient and safe operations, it is essential to protect and maintain the integrity of these pipelines. This is where oil pipeline liners come into play, with polyurea coatings playing a pivotal role in enhancing their durability and efficiency.
Oil Pipeline Liners: An Overview
Oil pipeline liners are protective coatings that are applied on the inner surfaces of pipelines to safeguard against corrosion, abrasion, and other potential damages. Corrosion, in particular, poses a significant threat to the structural integrity of pipelines, leading to leaks, spills, and increased maintenance costs. Therefore, the installation of liners is a proactive approach to preventing such issues and extending the lifespan of oil pipelines.
Polyurea: An Ideal Solution for Oil Pipeline Liners
Polyurea is a remarkable material that has gained popularity in various industries, including oil and gas. It is a two-component system that forms a strong, flexible, and impermeable membrane when applied. The exceptional qualities of polyurea make it an ideal choice for oil pipeline liners.
1. Corrosion Resistance:
One of the primary challenges that oil pipelines face is corrosion. Traditional coatings may provide some level of protection, but polyurea takes it a step further. Its chemical resistance properties enable it to withstand corrosive substances present in the transported oil, soil compounds, and even chemicals used in water treatment processes. With a polyurea liner, pipelines are shielded from corrosion, reducing the risk of leaks and maintaining oil flow efficiency.
2. High Abrasion Resistance:
Pipelines often encounter abrasions caused by solid particles, such as sand, rocks, or debris carried along with the oil during transportation. Polyurea coatings are highly resistant to abrasion, offering optimal protection against wear and tear. The robust nature of polyurea ensures that the pipelines can endure the harsh conditions within which they operate, thus minimizing maintenance requirements and downtime.
3. Flexibility:
Oil pipelines are buried underground or submerged in water bodies, making them susceptible to natural movements caused by shifting soil, seismic events, or temperature fluctuations. The flexibility of polyurea allows it to move and adjust with the pipelines, preventing cracks, leaks, or ruptures that may occur due to stress. This enhances the overall durability of the pipeline and ensures uninterrupted oil transportation.
4. Quick and Efficient Application:
Polyurea coatings can be applied rapidly and seamlessly, significantly reducing the downtime during the lining process. Unlike traditional coatings that may take several days to cure, polyurea cures within seconds or minutes, depending on the specific formulation. This efficiency in application allows for faster project completion, minimizing disruptions to oil production and transportation.
5. Longevity:
Oil pipeline liners with polyurea coatings have a long lifespan compared to other traditional coating systems. The combination of corrosion resistance, abrasion resistance, and flexibility ensures that the pipelines remain intact and functional for an extended period. The reduced need for repairs or replacements lowers maintenance costs and enhances the overall profitability of oil pipeline operations.
Conclusion
In the realm of oil pipelines, protecting and maintaining their integrity is of paramount importance. Oil pipeline liners, with their ability to withstand corrosion, abrasion, and environmental challenges, provide a proactive solution to this issue. Polyurea coatings, with their exceptional properties, offer an ideal protective layer for oil pipelines. From corrosion resistance to high flexibility and quick application, polyurea enhances the longevity, efficiency, and durability of oil pipeline liners. By utilizing polyurea coatings in oil pipeline infrastructure, the industry can ensure the safe and reliable transportation of petroleum products, ultimately contributing to a more sustainable energy future.
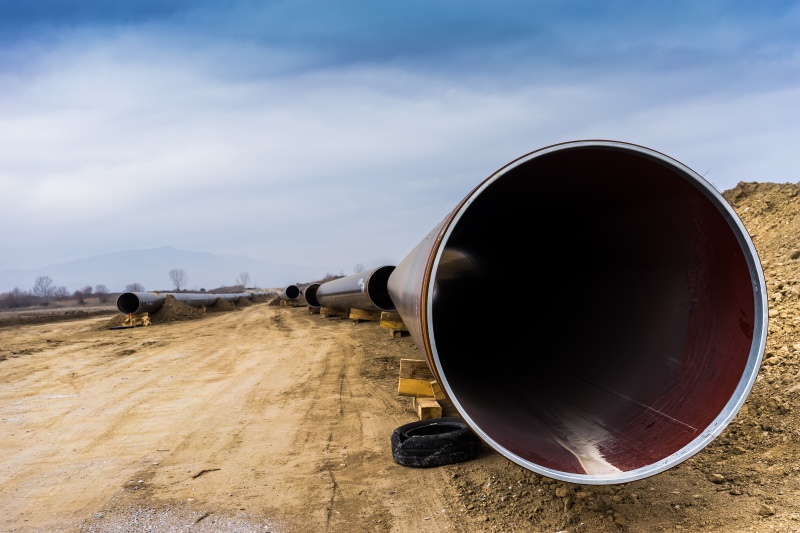