The pipeline integrity industry is crucial for ensuring the safe and efficient transportation of oil, gas, and other fluids. With thousands of miles of pipelines stretching across the globe, it’s essential to have robust systems in place to monitor and maintain their integrity. Artificial Intelligence (AI) is revolutionizing the way pipelines are managed, offering advanced solutions that enhance safety, reduce costs, and improve efficiency.
AI technology, including machine learning and data analytics, can be applied at various stages of the pipeline integrity management process. Let’s explore some of the key applications and benefits of using AI in the industry.
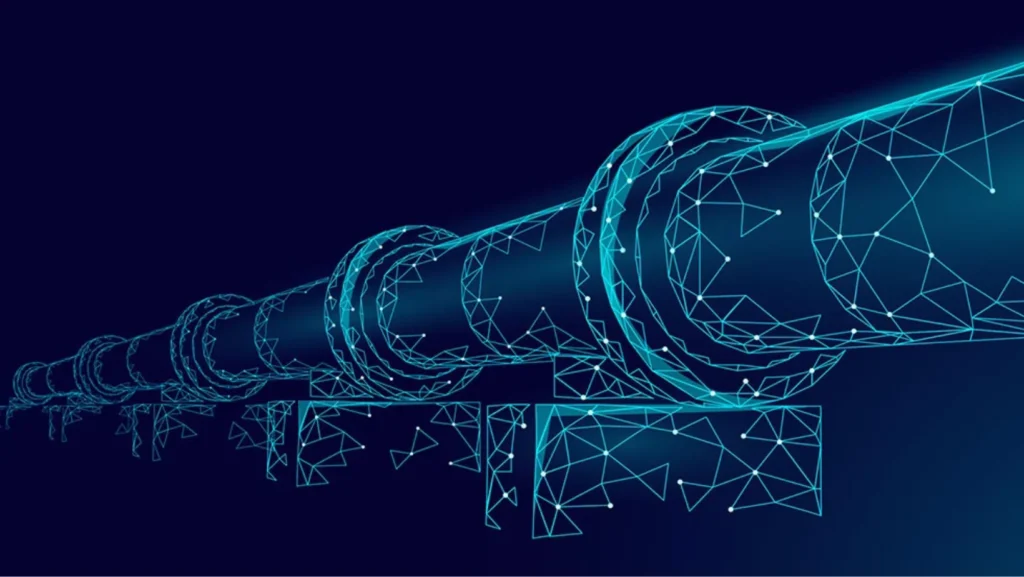
- Predictive Maintenance: AI can enable predictive maintenance by analyzing real-time data from sensors installed along the pipeline. By continuously monitoring parameters such as pressure, temperature, and flow rate, AI algorithms can identify patterns and anomalies that indicate potential issues. This proactive approach helps to prevent failures, reduce downtime, and optimize maintenance activities.
- Leak Detection: One of the most critical aspects of pipeline integrity is detecting leaks promptly. AI algorithms can analyze data from multiple sources, including acoustic sensors and satellite imagery, to identify leaks accurately. By comparing current data against historical patterns, AI can assess whether a leak exists, locate its precise position, and estimate its severity. Early detection of leaks improves environmental protection and minimizes the risk of accidents.
- Corrosion Monitoring: Corrosion is a significant threat to the integrity of pipelines, and timely detection is crucial to prevent catastrophic failures. AI systems can analyze data from corrosion sensors, cathodic protection systems, and other sources to identify areas prone to corrosion. Machine learning algorithms can predict corrosion rates based on historical data and provide recommendations for mitigating the problem. This proactive approach helps operators implement appropriate preventive measures and extend the lifespan of pipelines.
- Risk Assessment: AI can facilitate comprehensive risk assessments by analyzing vast amounts of data, including historical records, inspection reports, and environmental factors. Machine learning algorithms can identify potential risks, such as soil movement, natural disasters, or equipment aging, and calculate their likelihood and potential impact. This information allows operators to prioritize maintenance activities and allocate resources effectively, improving safety and cost savings.
- Pipeline Monitoring: AI-powered systems can continuously monitor pipelines using a combination of sensors, drones, and satellite imagery. Real-time data can be analyzed with historical information to detect anomalies, such as vibrations or temperature variations, that may indicate potential issues. Rapid identification of abnormal behavior allows for swift response, preventing accidents and minimizing the impact on operations.
- Decision Support: Integrating AI systems with existing pipeline integrity management software provides operator decision support capabilities. AI algorithms can analyze data, identify trends, and make predictive recommendations regarding pipeline maintenance, repairs, or replacement. This data-driven approach helps operators optimize their decision-making process, reduce costs, and improve overall pipeline integrity.
- Regulatory Compliance: The pipeline industry is subject to stringent regulations to ensure safety and environmental protection. AI can assist operators in complying with these regulations by providing accurate data analysis, reporting, and documentation. AI systems can automatically generate compliance reports, flag potential violations, and provide real-time information to regulatory authorities, streamlining the regulatory process and reducing administrative burden.
In conclusion, the use of AI in the pipeline integrity industry is transforming the way pipelines are monitored and managed. From predictive maintenance and leak detection to risk assessment and regulatory compliance, AI-powered systems offer significant benefits. By leveraging the power of AI, operators can enhance safety, reduce costs, optimize maintenance activities, and improve overall pipeline integrity. As technology continues to advance, the pipeline integrity industry can expect further improvements driven by AI innovations.