Oil pipelines play a crucial role in transporting vast amounts of oil across long distances, ensuring a steady supply to meet the world’s energy demands. However, these pipelines face various challenges, including corrosion, abrasion, and environmental factors, which can compromise their integrity and efficiency. That’s where oil pipeline coatings come in – serving as a vital defense system to protect and preserve these critical infrastructure assets.
Oil pipeline coatings are specialized materials applied to the external surface of pipelines to provide a barrier against corrosion, erosion, and other damaging elements. These coatings offer several benefits that help safeguard pipelines and extend their lifespan. Let’s explore some of the key advantages of oil pipeline coatings:
1. Corrosion Protection: Corrosion is a major concern for oil pipelines, as it can lead to leaks, ruptures, and environmental hazards. Pipeline coatings act as a protective layer, preventing corrosion by creating a barrier between the metal pipe and any corrosive agents present in the surrounding environment. Coatings can be made from various materials, including epoxy, polyurethane, or fusion-bonded epoxy (FBE), each offering different levels of corrosion resistance.
2. Abrasion Resistance: Oil pipelines often face challenges from the abrasive nature of the materials being transported. Coatings with high abrasion resistance properties can minimize the impact of these abrasive particles, reducing wear and tear on the pipeline surface. This helps to maintain the pipeline’s structural integrity and prevent costly repairs or replacements.
3. Environmental Protection: Oil pipelines frequently cross diverse environments, including challenging terrains and sensitive ecosystems. Pipeline coatings act as a protective shield against environmental factors such as moisture, chemicals, and extreme temperatures. By limiting direct contact between the pipeline and the surrounding environment, these coatings mitigate the risk of degradation or damage caused by these external factors.
4. UV Resistance: Above-ground pipelines are exposed to ultraviolet (UV) radiation from the sun. Continuous exposure to UV rays can lead to material degradation and premature aging of the pipeline. Specialized coatings with UV-resistant properties offer protection against these harmful rays, helping to maintain the structural integrity and visual appearance of the pipeline.
5. Enhanced Flow Efficiency: Coatings with smooth surfaces and low friction properties can contribute to improved flow efficiency within the pipeline. Reduced friction allows oil to flow more smoothly, reducing energy loss and ensuring a more efficient transportation process. This results in significant cost savings and increased operational efficiency for oil companies.
6. Easy Inspection and Maintenance: Pipeline coatings can be designed to have specific color variations or markings, aiding in visual inspection and maintenance programs. By easily identifying potential areas of concern, operators can monitor the pipeline’s condition, promptly address any issues, and implement maintenance measures to extend its service life.
In conclusion, oil pipeline coatings are a critical component in ensuring the longevity and integrity of oil transportation infrastructures. By providing a protective barrier against corrosion, abrasion, and environmental factors, these coatings help minimize the risk of leaks, reduce maintenance costs, and enhance the overall efficiency of the oil transportation process. Investing in high-quality pipeline coatings is essential to protect valuable assets and maintain a safe and reliable oil supply for years to come.
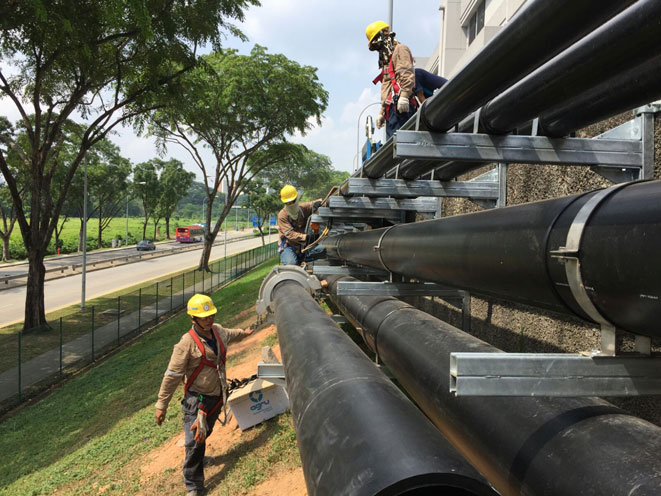