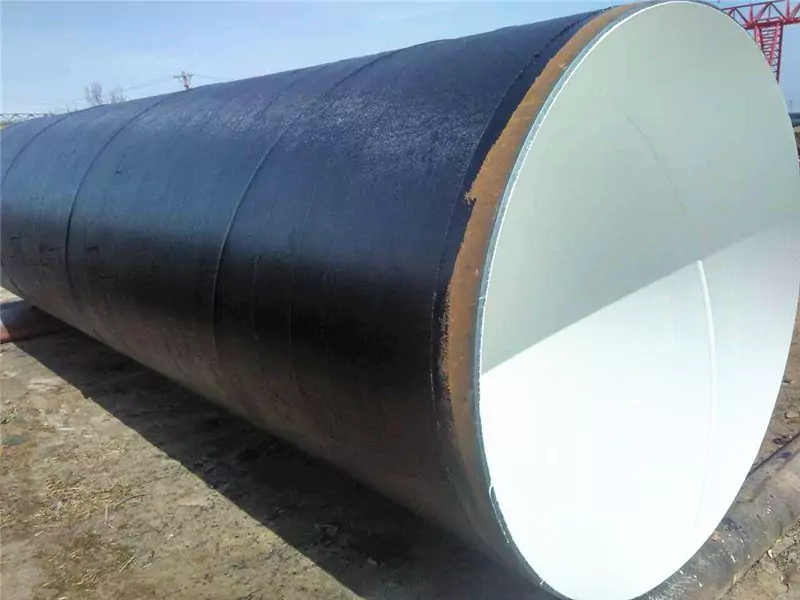
Protecting the Flow: The Role of Polyurea in the Oil Pipeline Industry
The oil pipeline sector plays a role in meeting the world’s energy needs by moving millions of barrels of oil every day across distances. These pipelines need to endure conditions and extreme weather to ensure a safe oil flow. To preserve their strength, it is crucial to protect them from rust, wear, and environmental harm. Polyurea, an adaptable coating, has emerged as a solution for providing this protection. This piece delves into the obstacles encountered by the oil pipeline industry and how polyurea helps safeguard this infrastructure.
The Importance of Pipeline Integrity
Pipelines serve as the lifelines of the oil industry, linking production sites to refineries, distribution hubs and consumers. These extensive networks stretch across continents traversing landscapes and climates. The uninterrupted functioning of pipelines is crucial, for maintaining the stability of energy markets and supporting the economies on them. Nevertheless,, the exposure of pipelines to elements like moisture, temperature fluctuations and chemical substances poses risks to their structural integrity.
Among the perils that pipelines encounter corrosion stands out as a threat. When metal pipelines come into contact with moisture and oxygen they undergo corrosion processes that result in rust formation and structural weakening. If left unaddressed corrosion can lead to leaks, breaches and in instances failures. These events not disrupt oil supply chains. Also present significant environmental dangers.
Additionally abrasion poses another obstacle for pipelines to contend with. As oil flows through the pipeline system it carries particles that gradually erode the walls of the pipes. This erosion over time can thin out the pipeline walls rendering them vulnerable to leaks and ruptures. External influences such as soil shifts or interaction, with rocks and debris can exacerbate abrasion issues further compromising the durability of pipelines.
Considering these dangers, safeguarding the reliability of pipelines is a concern within the oil sector. An efficient method to defend pipelines against risks involves the application of protective coatings. These coatings serve as a shield, safeguarding the pipeline from factors and prolonging its operational lifespan.
The Role of Polyurea in Pipeline Protection
Polyurea has become a choice for coating pipelines because of its characteristics. It is a spray-applied elastomer that quickly cures to form a flexible and highly resilient coating. Its ability to adhere to surfaces like metal, concrete, and plastic makes it an excellent option for safeguarding pipelines.
One of the benefits of using polyurea is its resistance to corrosion. When applied inside or outside a pipeline, polyurea acts as a watertight barrier that blocks moisture and oxygen from reaching the metal surface. This barrier effectively halts the corrosion process, preserving the pipeline’s integrity and reducing maintenance costs.
Another key feature of polyurea is its flexibility, which makes it suitable for protecting pipelines. Pipelines undergo movement due to temperature variations, ground shifts or material expansion and contraction. Unlike coatings that might crack or peel when subjected to stress polyurea can adapt to the pipelines movements while maintaining its qualities over time. This flexibility ensures that the coating remains intact, in conditions.
Additionally polyurea boasts abrasion resistance. The tough and durable layer this coating provides shields the pipeline from damage caused by oil flow and external elements.
By protecting against wear and tear polyurea plays a role, in prolonging the lifespan of pipelines reducing the chances of leaks and ensuring a flow of oil.
Another key advantage of polyurea is its curing process. Administered, polyurea solidifies rapidly enabling pipelines to resume operations. This speedy turnaround proves beneficial in the oil sector, where any downtime can lead to expenses. Additionally, the rapid curing time allows for polyurea application across conditions, making it a versatile solution for safeguarding pipelines.
Application and Maintenance of Polyurea Coatings
The use of polyurea coatings demands precision and expertise. Prior, to applying the coating it is crucial to clean and prepare the surface of the pipeline to ensure adhesion. This process may entail removing any rust, dirt or previous coatings that could hinder the bonding process. Once the surface is prepared specialized spray equipment is used to apply the polyurea ensuring an uniform coating.
A key advantage of polyurea lies in its quality. Unlike coatings that may necessitate joints or seams polyurea creates a layer that eliminates vulnerabilities where corrosion or leaks could arise. This seamless application not boosts the durability of the coating. Also streamlines maintenance since there are no seams requiring inspection or repair.
Regular upkeep plays a role in preserving the longevity of pipelines coated with polyurea. While polyurea is exceptionally resilient it’s still essential to inspect the coating for any signs of damage or wear. Any identified issues should be promptly addressed to prevent degradation and uphold the pipeline’s protection.
Advancements in polyurea technology have resulted in coatings with enhanced properties. For instance certain formulations are engineered to offer increased resistance, against UV radiation, chemical exposure or extreme temperatures.
These unique coatings provide protection, for pipelines in conditions prolonging their durability and minimizing maintenance requirements.
The Future of Polyurea in the Oil Pipeline Industry
As the oil pipeline sector progresses the use of polyurea coatings is expected to grow. Advances in creating formulations and applying techniques will improve the effectiveness and flexibility of polyurea, making it a more valuable asset for safeguarding pipelines.
The oil industry is increasingly concerned about sustainability. Polyurea coatings offer lasting protection. They also reduce maintenance needs, contributing to pipeline sustainability by minimizing environmental harm from leaks and cutting down on repair resources.
Apart from safeguarding existing pipelines polyurea is now being utilized in constructing pipelines. Its adaptability to conditions and environments makes it a practical option, for pipeline construction projects
Conclusion
Polyurea has become an essential component in protecting oil pipelines, offering a reliable and durable solution to the challenges of corrosion, abrasion, and environmental exposure. Its flexibility, rapid curing time, and resistance to harsh conditions make it a superior choice for maintaining pipeline integrity and ensuring the safe and continuous flow of oil. As technology advances and the demands on the oil industry continue to grow, polyurea will remain a critical tool in safeguarding the infrastructure that supports the global energy supply.
Learn more about pipeline coating options by visiting ArmorThane.com
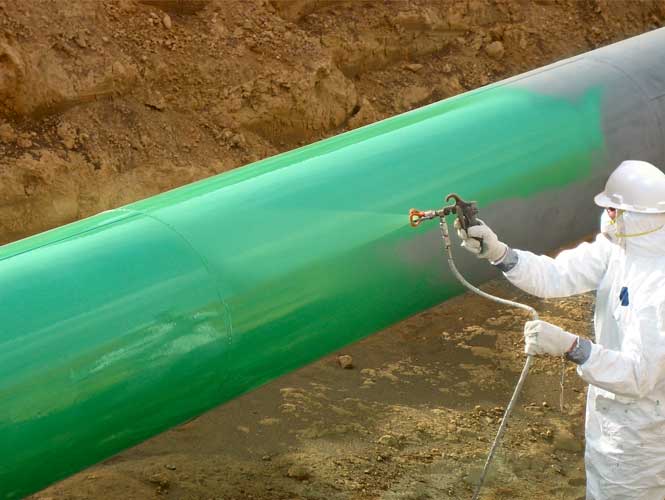
What are the Different Types of Oil Pipeline Coatings?
Understand the Benefits of Different Types of Oil Pipeline Coatings
Oil pipeline coatings are essential for protecting pipelines from external factors that can cause corrosion and damage. Different types of coatings offer different benefits for different applications, so it is important to understand the benefits of each type of coating before making a decision.
Polyethylene (PE) coatings are used for a wide variety of oil pipeline applications. These coatings offer excellent resistance to UV radiation and water absorption, making them ideal for outdoor applications. They also provide good abrasion resistance and are relatively easy to install. In addition, PE coatings are relatively inexpensive and have a long lifespan.
Epoxy coatings are also popular for oil pipelines. These coatings provide superior chemical resistance, making them ideal for applications where the pipeline is exposed to harsh chemicals. They also offer excellent adhesion and are relatively easy to apply. In addition, epoxy coatings are relatively inexpensive and provide a long lifespan.
Fusion bonded epoxy (FBE) is a type of epoxy coating that is often used for oil pipelines. FBE coatings offer excellent protection against corrosion and have good resistance to water, chemicals, and abrasion. These coatings are also relatively easy to install and can be used in a variety of applications.
Polyurethane (PU) coatings are an ideal choice for oil pipelines that need to be exposed to high temperatures. These coatings offer excellent thermal and chemical resistance, making them ideal for applications in which the pipeline is exposed to extreme temperatures and chemicals. In addition, PU coatings are relatively easy to install and provide a long lifespan.
When choosing a coating for an oil pipeline, it is important to consider the benefits of each type of coating and select the one that best meets the needs of the application. Each type of coating offers different benefits, so it is important to understand the benefits of each type before making a decision.
How to Choose the Right Oil Pipeline Coating for Your Project
The selection of an appropriate oil pipeline coating is an important part of a successful oil pipeline project. The type of coating used depends on the application, environmental conditions, and the type of oil being transported. It is important to select the correct coating to ensure the durability and performance of the pipeline.
When selecting the right pipeline coating, there are several factors to consider. The first is the application. Different coatings are available for different applications, such as internal or external pipelines, and for different types of pipe, such as carbon steel or plastic.
The environment in which the pipeline will operate also needs to be taken into consideration. Different coatings are designed to provide protection from corrosion in different environments, such as salty air or high humidity. It is important to choose the right coating to ensure the longevity of the pipeline.
The type of oil and chemicals being transported through the pipeline must also be taken into account. Different coatings are designed to protect against different types of oil and chemicals, so it is important to choose a coating that is compatible with the type of fluids being transported.
Finally, the cost of the coating must be taken into consideration. Different coatings have different costs, so it is important to consider the budget for the project when selecting a coating.
By selecting the right oil pipeline coating for your project, you can ensure the durability and performance of the pipeline. It is important to consider the application, environment, type of oil, and cost when selecting the right coating for your pipeline project.
An Overview of Common Oil Pipeline Coating Options
The use of oil pipelines is a common and efficient way to transport oil from one place to another. In order to ensure their longevity and effectiveness, they must be coated with a protective layer. There are several types of oil pipeline coating materials, each of which provides unique benefits. This article will provide an overview of the most common oil pipeline coating options.
Fusion-Bonded Epoxy (FBE) is a popular choice for oil pipeline coatings. This coating is applied as a powder and then heated to form a protective layer. FBE provides excellent corrosion protection and is highly resistant to chemicals, UV rays, and abrasion. It is also an effective barrier against microbial contamination.
Polyurethane is another common coating for oil pipelines. This material is applied as a liquid and provides excellent resistance to chemical attack, UV rays, and abrasion. It is also highly resistant to microbial contamination and has a long lifespan.
Polypropylene is another popular choice for oil pipeline coatings. This coating is applied as a powder and provides excellent corrosion protection, UV resistance, and thermal insulation. It is not as durable as FBE or polyurethane, but is still a reliable option.
Glass-Fiber Reinforced Plastic (GFRP) is a newer oil pipeline coating option. GFRP is applied as a liquid and provides excellent corrosion protection and thermal insulation. It is also resistant to UV rays and abrasion, making it an effective barrier against microbial contamination.
Finally, there are several other types of coatings used for oil pipelines, including asphalt, zinc, and galvanized steel. Asphalt provides good corrosion protection and is a cost-effective option. Zinc and galvanized steel are more expensive but provide superior corrosion protection.
No matter which type of coating is used, it is important to select the right option for the environment and the application. Each type of coating has its own benefits and drawbacks, so it is important to do research and speak to a knowledgeable professional before making a decision. Properly coating an oil pipeline is an essential part of ensuring its longevity and effectiveness.
Exploring the Advantages of Polyethylene and Fusion-Bonded Epoxy Coatings
Polyethylene and fusion-bonded epoxy coatings are two of the most effective and widely used coating systems for pipes and pipelines. Both of these coatings offer superior protection against corrosion and abrasion, making them ideal for a variety of industrial applications. In this article, we’ll explore the advantages of both polyethylene and fusion-bonded epoxy coatings, including their unique advantages over other coating systems.
Polyethylene is a highly durable and flexible material that can be applied to surfaces with a variety of methods. It is often used as a pipe coating because of its ability to resist corrosion, abrasion, and environmental conditions. Polyethylene is also highly resistant to chemicals, which makes it ideal for use in industrial settings. Additionally, polyethylene is cost-effective and easy to install.
Fusion-bonded epoxy (FBE) is a multi-layer coating system that is composed of a primer coat and a topcoat. It is applied through thermal spraying, which ensures that each layer is evenly distributed and securely bonded to the pipe surface. FBE is extremely resistant to corrosion and abrasion, making it a popular choice for pipelines in harsh environments. It is also highly resistant to chemicals and heat, and has a long lifespan.
When compared to other coating systems, polyethylene and FBE coatings have a number of advantages. For starters, they are both highly durable and resistant to corrosion, abrasion, and environmental conditions. Additionally, both polyethylene and FBE coatings are cost-effective and easy to install. Furthermore, polyethylene and FBE coatings are both highly resistant to chemicals, making them ideal for industrial applications.
Overall, polyethylene and fusion-bonded epoxy coatings are two of the most effective and widely used coating systems for pipes and pipelines. They offer superior protection against corrosion and abrasion, making them ideal for a variety of industrial applications. Additionally, they are both cost-effective and easy to install, and offer excellent chemical resistance. As such, these coatings are a great choice for any industrial setting.
Comparing the Different Protective Properties of Oil Pipeline Coating Materials
The oil industry relies on pipelines to transport its precious liquid cargo from one location to another. To ensure that these pipelines remain safe and reliable, they must be properly coated with materials that provide effective protection from corrosion, abrasion, weathering, and other environmental factors. Different types of coatings have varying levels of protective properties, so it is important to understand the differences between them.
One of the most common pipeline coating materials is polyethylene (PE). This material is highly resistant to corrosion, is lightweight, and is relatively cost-effective. It is also resistant to ultraviolet light and has low permeability, meaning that it is effective at keeping moisture and other contaminants out of the pipe.
Fusion-bonded epoxy (FBE) is another popular choice for pipeline coatings. It provides excellent protection against corrosion and is highly durable. FBE is more costly than PE, but it is also more resistant to weathering and abrasion.
A third option is liquid-applied epoxy (LAE). This material is more expensive than PE and FBE, but it offers superior corrosion protection. LAE also has low permeability, meaning that it can effectively keep moisture and contaminants out of the pipe.
Finally, polyurethane (PU) is a more expensive option compared to the others, but it offers superior protection from weathering, abrasion, and corrosion. PU is also highly flexible, making it ideal for pipelines in areas that experience extreme temperatures or seismic activity.
Each of these pipeline coating materials has its own unique set of protective properties, so it is important to consider what type of environment the pipeline will be operating in when making a selection. By understanding the differences between these materials, oil companies can ensure that their pipeline investments are protected for years to come.
Understanding the Different Types of Oil Pipeline Coatings
What You Need to Know About the Different Types of Oil Pipeline Coatings
Oil pipelines are an important part of the energy industry and are used to transport crude oil from one location to another. To ensure the longevity and efficiency of these pipelines, it is important to use the right type of coating. There are several different types of oil pipeline coatings available, each with its own advantages and disadvantages.
Epoxy coatings are one of the most popular types of coatings used for oil pipelines. This type of coating is resistant to corrosion and provides excellent protection from environmental elements. Epoxy coatings are also relatively easy to apply and are often used in areas where there is a high risk of corrosion.
Polyurethane coatings are another option for oil pipelines. These coatings are highly durable and provide excellent protection from the elements. They are also resistant to abrasion and can withstand high temperatures. They are often used in areas where there is a high risk of corrosion and extreme weather conditions.
Polyethylene coatings are designed to be lightweight and provide superior protection from corrosion. They are also resistant to abrasion and can withstand high temperatures. These coatings can be applied quickly and easily, making them a popular choice among oil pipeline operators.
Fusion-bonded epoxy coatings are a type of coating that is applied to the interior of the pipeline. This type of coating is highly resistant to corrosion and provides excellent protection from the elements. It is also highly resistant to abrasion and can withstand high temperatures. Fusion-bonded epoxy coatings are often used in areas where there is a high risk of corrosion and extreme weather conditions.
Finally, cathodic protection coatings are designed to protect pipelines from corrosion by providing a barrier between the pipe and the environment. These coatings are highly effective and can provide years of protection from corrosion. They are often used in areas where there is a high risk of corrosion and extreme weather conditions.
Each type of oil pipeline coating has its own advantages and disadvantages. It is important to consider the specific needs of the pipeline and the environment in which it will be used when selecting a coating. By taking all of these factors into consideration, the right type of coating can be chosen to ensure the longevity and efficiency of the pipeline.
Comparing the Benefits of Internal and External Pipeline Coatings
Internal and external pipeline coatings are used to protect pipelines from corrosion and other external factors. Both types of coatings have their own benefits and drawbacks, and it is important to understand the differences between them in order to choose the best option for a particular pipeline.
Internal pipeline coatings are applied on the inside of the pipe and can provide superior protection against corrosion caused by the chemicals or other substances that the pipeline carries. They also reduce the risk of fouling and blockage due to debris, which can lead to expensive repairs. Furthermore, internal coatings are relatively easy to apply and can provide long-term protection.
External pipeline coatings are applied to the outside of the pipeline and provide protection from external factors such as UV radiation, temperature changes, and corrosion caused by soil or water. They also provide an extra layer of protection from mechanical damage, such as impacts caused by construction or excavation. Moreover, external coatings are often used in combination with internal coatings for an extra layer of protection.
Both internal and external pipeline coatings have their own advantages and disadvantages, and the best option for a particular pipeline depends on its environment, use, and other factors. When choosing a coating, it is important to consider the cost of the coating, the type of protection it provides, and any potential maintenance requirements. Ultimately, the choice of coating should be based on a careful analysis of all the factors involved.
Exploring the Different Methods Used for Applying Oil Pipeline Coatings
Oil pipeline coatings are essential components of any oil pipeline infrastructure. They protect the pipe from corrosion, water damage, and other external factors. In order to ensure the longevity and performance of the pipeline, these coatings must be properly applied. There are a number of different methods used for applying oil pipeline coatings, and each has its own advantages and disadvantages.
One of the most common methods of applying oil pipeline coatings is by using a brush or roller. This method is relatively quick and inexpensive, and it can be used to apply relatively thin coatings. However, it is not suitable for pipelines that are exposed to harsh weather or high levels of stress, as the coating may not adhere properly. In addition, this method is not suitable for applying thicker coatings.
A more advanced method for applying oil pipeline coatings is powder coating. In this method, a special powder coating is applied to the pipe using a spray gun. This method is more expensive than using a brush or roller, but it is also much faster and results in a more uniform finish. This method is also suitable for applying thicker coatings, and is ideal for pipelines that are exposed to high levels of stress or harsh weather.
Other methods for applying oil pipeline coatings include extrusion coating and spray painting. Extrusion coating involves applying a melted coating material to the pipe using an extruder, and then cooling the material to form a protective coating. Spray painting is similar to powder coating, but instead of using a spray gun, a compressed air sprayer is used to apply the coating. This method is ideal for applying thin and even coatings, but it is not suitable for applying thicker coatings.
In addition to these methods, there are a number of other techniques that can be used to apply oil pipeline coatings. For example, liquid coatings can be applied using an airless sprayer, or a solvent can be used to penetrate the surface of the pipe before the coating is applied. Each of these methods has its own advantages and disadvantages, and the best method for a particular application will depend on the specific requirements of the project.
Whatever method is used for applying oil pipeline coatings, it is important to ensure that the coating is applied properly. If the coating is not applied correctly, it can lead to premature wearing and corrosion of the pipe, resulting in costly repairs or replacements. Therefore, it is essential to select the right method for each application in order to ensure the longevity and performance of the pipeline.
Investigating the Impact of Oil Pipeline Coating on the Environment
Oil pipelines are an essential part of the global energy infrastructure, responsible for transporting crude oil from production sites to refineries and other facilities. To ensure the safety and efficiency of the operation, it is important that the pipelines are adequately coated. However, the use of pipeline coatings can also have an impact on the environment, and it is essential to understand the potential effects so that appropriate steps can be taken to minimize any adverse impacts.
The primary environmental concern with oil pipeline coatings is that the materials used can leach pollutants into soil and water sources. These pollutants, which range from volatile organic compounds to heavy metals, can have a significant detrimental effect on local ecosystems. In addition, there is a risk of erosion and corrosion for pipelines not properly coated, leading to the release of hazardous materials into the environment.
To reduce the environmental impact of oil pipeline coatings, it is important to choose materials with low volatility and low toxicity. This is especially true for coatings used to line the inside of the pipeline, as these will come into direct contact with the oil and any pollutants it contains. It is also essential to ensure that the coating is applied in a manner that minimizes the risk of erosion or corrosion.
In addition to choosing the right materials and application methods, it is also important to consider the environmental effects of any waste generated during the coating process. For instance, many coatings release hazardous solvents during application, and these must be safely collected and disposed of to avoid their release into the environment.
Ultimately, the environmental impacts of oil pipeline coatings can be minimized through careful selection of materials and application methods. By taking these steps, it is possible to ensure that the pipeline is adequately protected while also reducing the risk of environmental damage.
Understanding the Regulations Surrounding the Use of Oil Pipeline Coatings
Oil pipelines are an important part of the global energy infrastructure, as they are used to transport oil from one location to another. As such, it is important to ensure that these pipelines are properly maintained and protected from corrosion and other damage. This is done by using a protective coating, which is applied to the outside of the pipeline to create a barrier between the metal and the environment.
The regulations surrounding the use of oil pipeline coatings vary from country to country, depending on the local laws and regulations. Generally speaking, the regulations aim to ensure that the coatings used are of a high quality and that they are applied in a safe and effective manner.
In the United States, the regulations governing the use of oil pipeline coatings are primarily set by the Pipeline and Hazardous Materials Safety Administration (PHMSA). This organization is responsible for overseeing the transportation of hazardous materials, including oil, and it sets standards for the safe transportation of these materials. In particular, the PHMSA issues regulations on the use of coatings, specifying the types of coatings that must be used, the thickness of the coating, and the application method.
In addition to the PHMSA regulations, a number of other organizations also have standards and guidelines for the use of oil pipeline coatings. The American Petroleum Institute (API) provides a number of standards and guidelines for the use of coatings, including the API 5LX standard, which provides guidance on the selection and application of protective coatings. The National Association of Corrosion Engineers (NACE) also has a number of standards related to the use of protective coatings, including the NACE SP0169 standard, which provides guidance on the selection and application of coatings for oil pipelines.
Finally, it is important to note that the regulations governing the use of oil pipeline coatings may also vary depending on the type of pipeline being used. For example, pipelines that are used to transport hazardous liquids may have different coating requirements than those used for transporting non-hazardous liquids.
By understanding the regulations surrounding the use of oil pipeline coatings, companies can ensure that their pipelines are properly protected and that they are in compliance with all applicable regulations. This will help to ensure that pipelines are safe to use and that they can continue to transport oil for many years to come.
The Advantages of Protective Coatings for Oil Pipelines
Protect Your Assets with Protective Coatings on Oil Pipelines
It is very important to protect oil pipelines from corrosion and other external factors that can damage them. Protective coatings are a important tool that is used to prevent corrosion and other damage to oil pipelines. These coatings act as a shield between the pipe and the environment thus increasing the pipeline’s service life.
There are many types of protective coatings that are offered to fit the needs of each pipeline. These coatings can be in the form of tapes, wraps or liquid applied coatings. One of the most common types of pipeline protective coating is polyethylene tape wrap. This kind of coating is wrapped in the form of continuous tape on the pipe. It is very efficient in preventing corrosion, UV and abrasion damage.
Protective coatings are a necessary means of protecting oil pipelines against corrosion and other forms of damage that occur due to environmental conditions. These coatings act as a shield between the pipe and the environment and reduce the chances of corrosion, thus increasing the pipeline’s lifespan. It is necessary to determine the specific requirements of an oil pipeline and its surroundings before selecting a protective coating for the pipeline.
Keep Your Oil Pipelines Running Smoothly with Protective Coatings
Oil pipelines are vital assets in the energy sector, transporting oil and gasoline from production and refining centers to marketing centers. Certain measures must be taken to prevent corrosion and wear in these pipelines. One of the best ways to achieve this is through the application of coatings.
Before applying the protective coatings, the first step is to ensure that the surface to be coated is clean and free from dust, grease, or other loose material. Sand blasting or chemical stripping is sometimes used to remove any residue on the surface. Only after the surface is ready can the protective coating be applied.
There are various types of protective coatings including paint, primer, and epoxy. Each of these has its own advantages, so it is crucial to select the appropriate one for the area to be coated. For instance, paint is used to prevent corrosion while epoxy is ideal for high wear areas and offers extra strength and flexibility.
After applying the protective coating, it is recommended that the area be checked on a regular basis to determine its effectiveness. This may involve looking for any indications of damage such as chipping or flaking which may indicate that the coating is not effective. It is also crucial to ensure that chemicals or any other agents are not attacking the coating in the environment.
This, in turn, can result in the company losing a lot of time and money, which can be avoided by protecting oil pipelines with protective coatings. Thus, protective coatings can help preserve oil pipelines and make them last for many years.
Discover the Lasting Benefits of Protective Coatings on Oil Pipelines
Protective coatings for oil pipelines offer a wide range of benefits that can extend the life of a pipeline and protect it from damage. These coatings are designed to protect the pipe from corrosion, abrasion, and other environmental factors. As a result, they can help reduce maintenance and repair costs, increase the pipeline’s safety, and ensure its long-term integrity.
One of the most important benefits of protective coatings for oil pipelines is their ability to protect the pipe from corrosion. By creating a barrier between the pipe and the environment, these coatings can help prevent corrosion from occurring. This can extend the lifespan of the pipe and reduce the need for costly repairs. In addition, protective coatings can also help reduce the risk of leaks and spills by providing an extra layer of protection against external elements.
Abrasion is another factor that can cause damage to oil pipelines. Protective coatings can help reduce the wear and tear that can occur over time, protecting the pipeline from abrasive forces. This can help extend the life of the pipeline and reduce the risk of failure due to wear and tear.
Another benefit of protective coatings is their ability to protect against environmental factors such as UV radiation, extreme temperatures, and moisture. These coatings can help insulate the pipe from these elements, protecting it from the effects of weathering and damage. This can help ensure the long-term integrity of the pipeline.
Finally, protective coatings can also help reduce the risk of damage caused by human activity. By providing an extra layer of protection, these coatings can help reduce the risk of accidents and vandalism, ensuring the pipeline’s safe operation.
In conclusion, protective coatings for oil pipelines can provide a range of benefits that can extend the life of the pipeline, reduce maintenance and repair costs, and improve the safety of the pipeline. By providing an extra layer of protection against corrosion, abrasion, and environmental factors, these coatings can help ensure the long-term integrity of the pipeline.
Maximize the Life of Your Oil Pipelines with Protective Coatings
Oil pipelines are essential to our energy infrastructure, transporting oil and gas to where it’s needed. Regular maintenance and protection are necessary to ensure your pipeline is working safely and efficiently. Protective coatings are an effective way to extend the life of oil pipelines, protecting them from a variety of environmental conditions.
Protective coatings provide a barrier between the pipeline and its environment, shielding it from rusting, corrosion, and other forms of damage. The right coating can ensure the pipeline is able to withstand the toughest conditions, including extreme temperatures, humidity, and sunlight. Additionally, protective coatings can protect against mechanical damage caused by soil movement or heavy equipment.
There are several types of protective coatings available, each of which offers a different level of protection. For instance, epoxy coatings are designed to increase the resistance of the pipe to corrosion and abrasion, while polyurethane coatings provide superior protection against UV rays and other weather-related damage.
When selecting a protective coating for your oil pipeline, it’s important to consider the conditions it will be exposed to. For example, if the environment is especially harsh, you may need a more robust coating. Additionally, the coating should be chosen based on the diameter and material of the pipeline, as well as any other special requirements.
By investing in protective coatings for your oil pipeline, you can extend its life and ensure it continues to operate safely and efficiently. With the right protective coating in place, you can rest assured that your pipeline will be able to withstand the toughest environmental conditions.
How Protective Coatings Can Help You Get the Most Out of Your Oil Pipelines
Protective coatings play an essential role in maintaining the structural integrity of oil pipelines. These coatings protect the pipelines from various environmental elements and corrosion, which can lead to costly repairs and downtime. In addition to providing superior protection, coatings can also help to extend the life of the pipeline, reducing maintenance costs and increasing the efficiency of the system.
The most common type of protective coating used on oil pipelines is a polyurethane-based coating. This type of coating offers excellent protection from corrosion, UV radiation, and other environmental elements. The coating is applied in multiple layers, depending on the level of protection required, ensuring that the pipeline is adequately protected.
In addition to providing superior protection against corrosion and environmental elements, coatings can also help reduce friction, which can lead to improved flow efficiency. This can result in improved operational performance and savings in energy costs. Coatings can also help to reduce noise caused by the flow of oil, making it easier to operate the pipeline in populated areas.
A major benefit of using protective coatings on oil pipelines is that they can help to reduce the risk of leaks and spills. By providing an additional layer of protection, coatings can help to contain leaks and reduce the impact of any potential spills. This can result in improved environmental safety and fewer liabilities for the pipeline operators.
Finally, protective coatings can help reduce maintenance costs by making it easier to inspect the pipelines and identify potential issues before they become serious. By providing an additional layer of protection, coatings can help to reduce the need for repairs and potentially save money in the long run.
In conclusion, protective coatings are essential for maintaining the structural integrity of oil pipelines. These coatings can provide superior protection against corrosion and environmental elements, reduce friction, and reduce the risk of spills and leaks. They can also help to reduce maintenance costs by making it easier to identify potential issues before they become serious. By taking advantage of the benefits of protective coatings, operators can get the most out of their pipelines and save money in the long run.
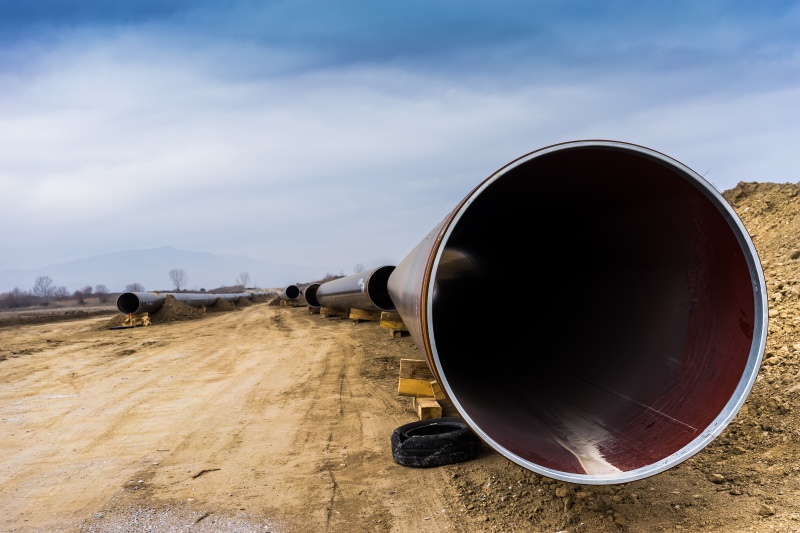
Oil Pipeline Liners: Enhancing Efficiency and Durability with Polyurea Coatings
Oil pipelines play a crucial role in the transportation of petroleum products from the extraction sites or refineries to various distribution centers. These pipelines span vast distances and are subjected to extreme conditions and environmental challenges. To ensure efficient and safe operations, it is essential to protect and maintain the integrity of these pipelines. This is where oil pipeline liners come into play, with polyurea coatings playing a pivotal role in enhancing their durability and efficiency.
Oil Pipeline Liners: An Overview
Oil pipeline liners are protective coatings that are applied on the inner surfaces of pipelines to safeguard against corrosion, abrasion, and other potential damages. Corrosion, in particular, poses a significant threat to the structural integrity of pipelines, leading to leaks, spills, and increased maintenance costs. Therefore, the installation of liners is a proactive approach to preventing such issues and extending the lifespan of oil pipelines.
Polyurea: An Ideal Solution for Oil Pipeline Liners
Polyurea is a remarkable material that has gained popularity in various industries, including oil and gas. It is a two-component system that forms a strong, flexible, and impermeable membrane when applied. The exceptional qualities of polyurea make it an ideal choice for oil pipeline liners.
1. Corrosion Resistance:
One of the primary challenges that oil pipelines face is corrosion. Traditional coatings may provide some level of protection, but polyurea takes it a step further. Its chemical resistance properties enable it to withstand corrosive substances present in the transported oil, soil compounds, and even chemicals used in water treatment processes. With a polyurea liner, pipelines are shielded from corrosion, reducing the risk of leaks and maintaining oil flow efficiency.
2. High Abrasion Resistance:
Pipelines often encounter abrasions caused by solid particles, such as sand, rocks, or debris carried along with the oil during transportation. Polyurea coatings are highly resistant to abrasion, offering optimal protection against wear and tear. The robust nature of polyurea ensures that the pipelines can endure the harsh conditions within which they operate, thus minimizing maintenance requirements and downtime.
3. Flexibility:
Oil pipelines are buried underground or submerged in water bodies, making them susceptible to natural movements caused by shifting soil, seismic events, or temperature fluctuations. The flexibility of polyurea allows it to move and adjust with the pipelines, preventing cracks, leaks, or ruptures that may occur due to stress. This enhances the overall durability of the pipeline and ensures uninterrupted oil transportation.
4. Quick and Efficient Application:
Polyurea coatings can be applied rapidly and seamlessly, significantly reducing the downtime during the lining process. Unlike traditional coatings that may take several days to cure, polyurea cures within seconds or minutes, depending on the specific formulation. This efficiency in application allows for faster project completion, minimizing disruptions to oil production and transportation.
5. Longevity:
Oil pipeline liners with polyurea coatings have a long lifespan compared to other traditional coating systems. The combination of corrosion resistance, abrasion resistance, and flexibility ensures that the pipelines remain intact and functional for an extended period. The reduced need for repairs or replacements lowers maintenance costs and enhances the overall profitability of oil pipeline operations.
Conclusion
In the realm of oil pipelines, protecting and maintaining their integrity is of paramount importance. Oil pipeline liners, with their ability to withstand corrosion, abrasion, and environmental challenges, provide a proactive solution to this issue. Polyurea coatings, with their exceptional properties, offer an ideal protective layer for oil pipelines. From corrosion resistance to high flexibility and quick application, polyurea enhances the longevity, efficiency, and durability of oil pipeline liners. By utilizing polyurea coatings in oil pipeline infrastructure, the industry can ensure the safe and reliable transportation of petroleum products, ultimately contributing to a more sustainable energy future.
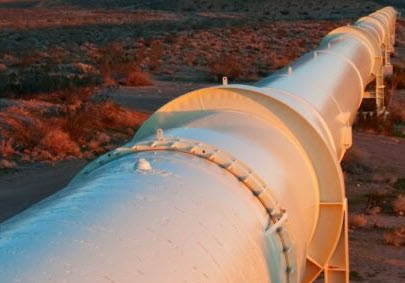
Oil Pipeline Coatings: Protecting our Energy Infrastructure
In today’s modern society, energy plays a crucial role in our daily lives. We rely on a constant supply of oil to power our vehicles, heat our homes, and fuel our industries. And at the heart of this energy supply chain are the vast networks of oil pipelines that crisscross the globe. These pipelines serve as the lifelines of the energy industry, transporting oil from production sites to refineries and distribution centers. However, for these pipelines to function effectively and safely, they require a crucial element – protective coatings.
Oil pipeline coatings are an essential component of the energy infrastructure, ensuring the durability, longevity, and safety of these vital conduits. These coatings serve a multitude of purposes, including corrosion prevention, insulation, and enhanced flow efficiency. Let’s delve deeper into the significance of oil pipeline coatings and their various types.
Corrosion prevention is the primary function of pipeline coatings. As pipelines are exposed to harsh environmental conditions, including moisture, soil, and chemicals, they are susceptible to corrosion. Corrosion not only weakens the structural integrity of pipelines but can also lead to leakage, spills, and environmental hazards. To combat this, pipeline coatings act as a barrier, protecting the steel surface from corrosion agents. These coatings consist of materials like epoxy, polyethylene, and polyurethane, which create a physical barrier that keeps corrosive elements away from the pipeline material.
In addition to corrosion prevention, coatings also act as insulation for pipelines. Oil pipelines often carry oil at high temperatures, and without proper insulation, significant energy loss can occur. Coatings made from thermally insulating materials like polyurethane foam can minimize heat dissipation, ensuring that the oil remains at optimal temperatures during transportation. This not only improves energy efficiency but also reduces the risk of oil freezing in colder regions, which can cause blockages and hinder the flow of oil.
Furthermore, oil pipeline coatings can enhance the overall efficiency of the pipeline system. The smooth surface created by coatings reduces friction, enabling oil to flow more efficiently through the pipeline. This not only increases the volume of oil that can be transported but also reduces the energy required for pumping, resulting in cost savings and a more sustainable operation.
There are different types of oil pipeline coatings available, each with its unique characteristics and advantages. Fusion-bonded epoxy (FBE) coatings are commonly used due to their excellent adhesion properties, chemical resistance, and high-temperature resistance. They are applied as a powder and then melted onto the pipeline surface.
Another commonly used coating is three-layer polyethylene (3LPE). This coating combines the benefits of a fusion-bonded epoxy layer, an adhesive layer, and a high-density polyethylene outer layer. The 3LPE coating provides excellent corrosion resistance, impact resistance, and UV protection.
Polyurethane coatings are also utilized for their exceptional mechanical properties and resistance to abrasion. These coatings are often applied as a topcoat to provide additional protection to the underlying layers.
It is worth noting that the application of pipeline coatings is a meticulous process that requires skilled professionals and adherence to strict quality control measures. Surface preparation, including cleaning and removing any rust or debris, is crucial to ensure proper coating adhesion. Additionally, regular inspection and maintenance are necessary to identify any coating damage or degradation and initiate timely repairs.
In conclusion, oil pipeline coatings play a vital role in safeguarding our energy infrastructure. These coatings protect pipelines from corrosion, insulate against heat loss, and enhance the overall efficiency of oil transportation. By investing in high-quality pipeline coatings, we can ensure a reliable, safe, and sustainable energy supply, supporting our modern way of life.